Každý transformátor, ať suchý nebo olejový, pracuje s magnetismem. Každá změna elektrického pole kolem vodiče vyvolává změnu pole magnetického a opačně. K vedení magnetického toku se dnes nejvíce používají ocelové magnetické plechy, kterými se jednotlivé cívky vzájemně vnitřně propojí. Takto vytvořená soustava se vzájemně ovlivňuje. Magnetickému obvodu říkáme jádro a je srdcem transformátoru.
Díky výzkumu a vývoji výrobců oceli a transformátorů, byly vyvinuty materiály s vylepšenými vlastnostmi spolu s lepšími technologiemi pro jejich zpracování. Dříve byly pro výrobu používány plechy s mnohem horšími vlastnostmi a oproti dnešním standardům byly spojeny s vysokými ztrátami a magnetizačním výkonem. Později bylo zjištěno, že přidáním křemíku (4 – 5 %) do slitiny oceli výrazně zlepšilo charakteristiky materiálu v důsledku zvýšení elektrického odporu a permeability.
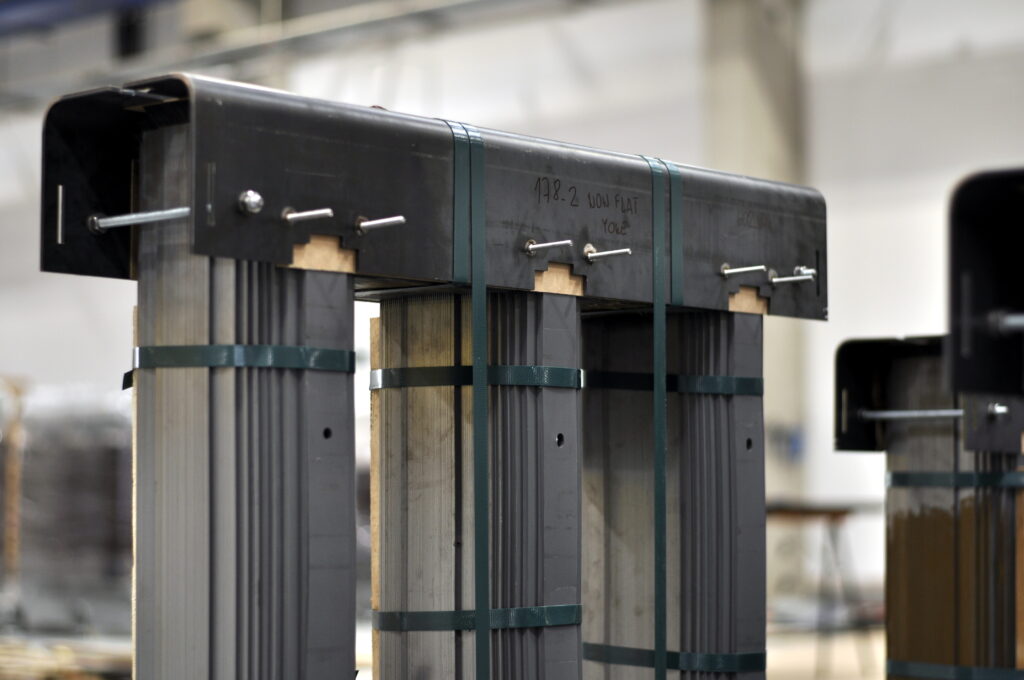
Snížily se i ztráty hysterezní, díky zmenšení plochy B-H smyčky. Od té doby jsou křemíkové oceli používány u většiny transformátorů. Přidání křemíku navíc napomáhá pomalejšímu stárnutí, ačkoliv křemík činí materiál křehčí, ale ne v takové míře, aby to působilo problémy při skládání plechů.
Následně byla zavedena technologie s válcováním plechů za studena, kde jsou zrna materiálu orientované ve směru válcování. Zpracování probíhá tak, že se optimální vlastnosti vyvíjejí ve směru válcování díky přísné kontrole orientace magnetických domén vzhledem k plechu (navržené Normanem P. Gossem). V tomto směru má lepší vlastnosti jako jsou snížené ztráty v železe a malá magnetostrikce. Ve směru válcování narostla magnetická indukce podle o 30 %, ačkoliv magnetické nasycení kleslo o 5 %. Proto je orientovaná ocel vhodná primárně pro transformátory nikoliv pro magnetické obvody motorů.
Materiály různé kvality byly historicky představeny v následujícím pořadí: neorientované, za tepla válcované orientované plechy (HRGO – hot-rolled grain-oriented), za studena válcované orientované plechy (CRGO – cold-rolled grain-oriented), za studena válcované orientované plechy s vysokou permeabilitou (Hi-B – high permeability cold-rolled), mechanicky nebo laserem stříhané. Dnes jsou nejběžněji používané Hi-B plechy, výroba oproti CRGO je zjednodušena eliminací jedné etapy válcování kvůli přidání přibližně 0,025 % hliníku do taveniny. Hi-B plechy mají měrné ztráty menší o 15-20 % než běžné CRGO. Ztráty se ještě dají snížit o 5-8 % laserovou úpravou, kde jsou magnetické domény více rozděleny.
Pro snížení vířivých ztrát se používají plechy s malou tloušťkou, aktuálně se tloušťka u výkonových transformátorů pohybuje v rozmezí od 0,23 mm do 0,35 mm, zatímco u malých transformátorků se používá tloušťka až 0,50 mm. Je potřeba vzít v potaz, že čím menší tloušťka, tím se prodlužuje čas skládání jádra, protože počet plechů pro dosažení požadovaného průřezu roste. Tyto plechy mohou pracovat s magnetickou indukcí až do 1,75 T. EcoDesign svým zavedením automaticky omezuje použití kvality transformátorového plechu na min. M085-23, se ztrátovým číslem 0,85 W/kg při indukci 1,7 T, v tomto příkladu s tloušťkou 0,23 mm.
Plechy jsou pokryty anorganickou izolační vrstvou typicky šedé barvy, zvané Carlite. Je to finální úprava povrchu transformátorového plechu. Jedná se o 2-4 µm silnou vrstvu vznikající na obou stranách plechu chránící před přídavnými vířivými proudy. Skládá se ze dvou vrstev, základní C2 (skelný film), vznikající jako chemická reakce povrchu za vysokoteplotního žíhání s MgO a přetvářející se na Mg2SiO4. Po konečném očištění dalším žíháním (800-850°C) se nanáší finální fosfátová vrstva C5. Izolace je dostatečná, aby odolala indukovaným napětím o velikosti několika voltů.
Jelikož je jádro v blízkosti vinutí vysokého napětí, je uzemněno, jinak může získat vysoký potenciál v důsledku kapacitně přenášeného napětí z vinutí. Pokud je jádro z důvodu chlazení rozděleno kanály (o tloušťce asi 5 mm), musí být jednotlivé sekce uzemněny. Vzhledem k tomu, že kapacita mezi kterýmikoliv dvěma sousedícími plechy je velmi velká kvůli jejich velké ploše a velmi malé izolační mezeře mezi nimi, je kapacitní reaktance mezi nimi zanedbatelná. Proto všechny plechy v jedné sekci zůstávají téměř na stejném potenciálu. A tudíž je každá z částí uzemněna pouze v jednom bodě.
Konstrukční uspořádání magnetického obvodu
Pro olejové distribuční transformátory se využívá téměř výhradně jádrového trojfázového uspořádání magnetického obvodu, viz obr. 1. Z ekonomického hlediska a větším rozměrům se plášťový typ (obr. 1b) vůbec nevyplatí, snad jen u pecních transformátorů.
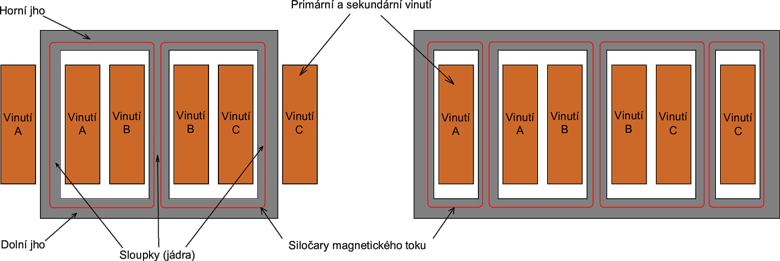
Obr. 1 a) Jádrové uspořádání trojfázového transformátoru b) Plášťové uspořádání trojfázového transformátoru
Magnetický tok každé fáze se uzavírá přes sloupek a vrací se jhy a zbylými dvěma sloupky. Průřez sloupku a jha bývá většinou stejný, je to i jednodušší při vysekávání jádra, protože se souvisle vysekává jedna vrstva ze stejného svitku plechu. Teoreticky by se dalo zvětšením průřezu jha docílit nižších ztrát naprázdno, ale kvůli nerovnosti průřezů mohou ztráty opět narůst z důvodu horších spojů mezi sloupky a jhy, snížení ztrát tedy nebude efektivní. Jádrová konstrukce trojfázového transformátoru má vlastní trojfázovou nesymetrii způsobenou nerovnoměrně rozloženého proudu naprázdno mezi fázemi. Proudy ve fázích A:B:C jsou v přibližně v poměru 1 : 0,718 : 1, kde B je prostřední sloupek. Tato nerovnost je způsobená delší magnetickou cestou pro krajní sloupky, když se na délku magnetického obvodu podíváme z hlediska každé fáze samostatně. Symetrického jádra by se dalo docílit spojením sloupků do trojrozměrné hvězdy nebo trojúhelníku, tak že by vinutí mezi sebou mechanicky svírala úhel 120°, ale z hlediska výroby je takové provedení zbytečně složité.
U velkých výkonových, suchých a dřívějších distribučních olejových transformátorů bývají plechy jádra poskládány tak, aby vytvořily co nejvíce kruhovitý průřez, aby se dosáhlo maximálního využití prostoru uvnitř válcovitých vinutí. Stupňovitý průřez se blíží kruhovému tvaru pouze v závislosti na tom, kolik různých šířek plechu má výrobce připraven k vysekávání. U distribučních transformátorů se počet stupňů pohybuje v rozmezí od pouhých 5 až po 10 nebo více. Tvar jádra pak využívá přibližně 88% respektive 95 % plochy kruhu. Ve skutečnosti může být využití plochy lehce nižší, protože výrobci si kladou za cíl standardizovat rozsah šířek plechů pro pokrytí všech různých velikostí jader, nebo si může kupovat materiál již nařezaný, v takovém případě bude standardní rozsah šířek poskytovaný výrobcem elektrotechnické oceli omezen, obvykle jsou odstupňovány po 10 mm např. od 50 mm po 440 mm šířky (dáno omezením vysekávacího stroje). Za takových podmínek je nepravděpodobné, že budou dostupné šířky pro optimální zaplnění jádra pro každý poloměr při daném počtu stupňů.
Maximální využití prostoru samozřejmě nabízí čtvercový či obdélníkový tvar jádra a vinutí zároveň, kdy navíc stačí jedna šířka použitého plechu, ale síly mezi vinutími vyvolané zkratovým proudem, které na takový tvar v kritických místech působí, jsou příliš velké. Běžně používaná technologie ale pro zpevnění vinutí nestačí, aby se zabránilo nežádoucí deformaci. Porovnání působení zkratových sil mezi vinutími je k nahlédnutí na obr. 2.
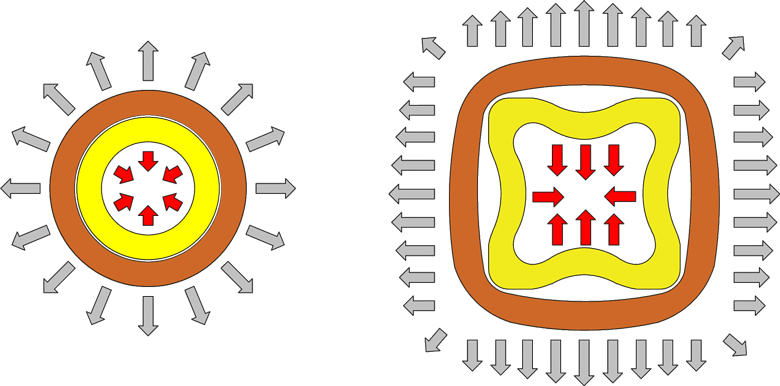
Obr. 2 Působení zkratových sil na kruhový a obdélníkový tvar vinutí
V posledních letech je však trendem používat jádro a také vinutí oválného tvaru v průřezu. U takového provedení je klasické kruhové jádro rozdělné na dvě poloviny a mezi ně je přidán další stupeň, který představuje rovnou část (vizuální demonstrace na obr. 3.). Dobře si pamatujeme dobu, kdy velmi stoupla cena mědi a výroba vinutí byla výhodnější z hliníku. Aby však byly zachovány stejné ztráty, transformátory narostly ve váze i v rozměrech, což se neslučovalo s maximálními technickými specifikacemi energetických společností. Oválný design vyžadoval inovativní a složitější technologii navíjení, jako je oválný rozpínací trn, pohyblivé válečky v navíjecím stroji pro zajištění pevnosti a dynamické regulaci tažení drátu pro zajištění maximální rychlosti navíjení a zároveň požadované přesnosti parametrů vinutí. Bylo také nutné provést nové typové zkoušky, přes které nový design úspěšně prošel. Jelikož u oválného designu zkratové síly působí destruktivněji než u kruhového, aby vinutí zafixovaná vytvrzenou izolací napuštěnou pryskyřicí mechanicky vydržela s rezervou, doporučuje se tloušťkou rovné části nepřesáhnout 100 mm. Oválné jádro a vinutí je zobrazeno uprostřed na obr. 3.
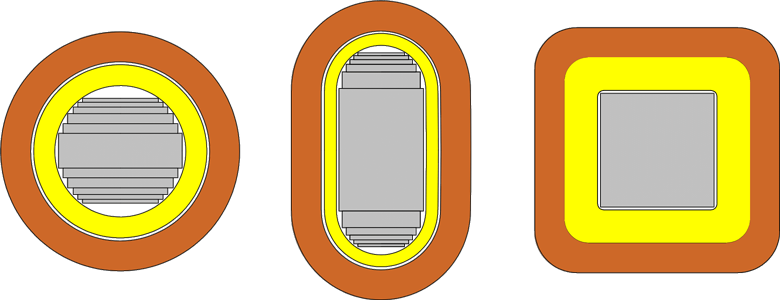
Obr. 3 Průřez jádra a vinutími různých tvarů, zleva kruhový, oválný a čtvercový tvar
Co se týče tvaru průřezu jha distribučních olejových transformátorů, na rozdíl od sloupku již není trendem dosáhnout symetrického tvaru (např. u suchých má i jho stejný oválný průřez jako sloupek). Je ale snaha přeskládat plechy stejné šíře jako ve sloupku tak, aby tvořily rovnou hranu na straně směrem k vinutím. Sníží se tak hmotnost magnetického obvodu a lehce sníží ztráty. Jen poslední jeden až dva stupně jsou v rámci šířky vycentrovány se stupněm předchozím, a to jen kvůli snadnějšímu zakládání a stlačování plechů jha, viz obr. 4.

Obr. 4 Porovnání poskládání plechů v průřezu sloupku a jha
Podíl mezi ztrátami smontovaného magnetického obvodu a hmotností magnetického obvodu vynásobeného měrnými ztrátami je známý jako činitel přídavných ztrát naprázdno. Hodnota tohoto činitele je důležitá při správném výpočtu ztrát naprázdno jakéhokoliv výkonového nebo distribučního transformátoru. Jedná se o empiricky odvozeného činitele, který je založen na zkušenostech výrobce transformátorů a pohybuje se od 1,08 do 1,35 pro třífázové jádrové magnetické obvody. Činitel přídavných ztrát naprázdno je bezrozměrná veličina a záleží na mnoha faktorech, jako je jakost materiálu plechů, lidský faktor při skládání plechů, a především geometrie magnetického obvodu, tj. poměr objemu rohových spojů k celkovému objemu magnetického obvodu. Pročež pro transformátory malých výkonů (25 kVA až 100 kVA) se činitel pohybuje v rozmezí až 1,25 do 1,35, zatímco pro transformátor nad 25 MVA bude činitel relativně nižší od 1,08 do 1,15. Hodnota činitele stavby teda klesá s rostoucím výkonem, protože větší výkon má výrazněji větší poměr mezi objemem jádra a objemem ve spojích, díry jsou také relativně menší. Jelikož z největší části rozhoduje o velikosti činiteli přídavných ztrát naprázdno spoj mezi plechem sloupku a jha, můžeme provést jeho rozdělení v následující kapitole.
Dělení jader z hlediska skládání plechů
Nezkosený spoj s úhlem hrany 90° je jednodušší z hlediska výroby, ale protože jsou ve spojích větší ztráty, používají se jen pro malé transformátory. Spolu s neorientovanými plechy však byly používány i u transformátorů velkých výkonů.
U orientovaných plechů, aby se do určité míry omezilo odbočení magnetického toku od směru orientace plechu ve spojích mezi sloupky a jhy, je lepší stříhat pod úhlem 45°, což je nejpoužívanější varianta. Úhel zkosení se však může pohybovat i od 30° do 60°.
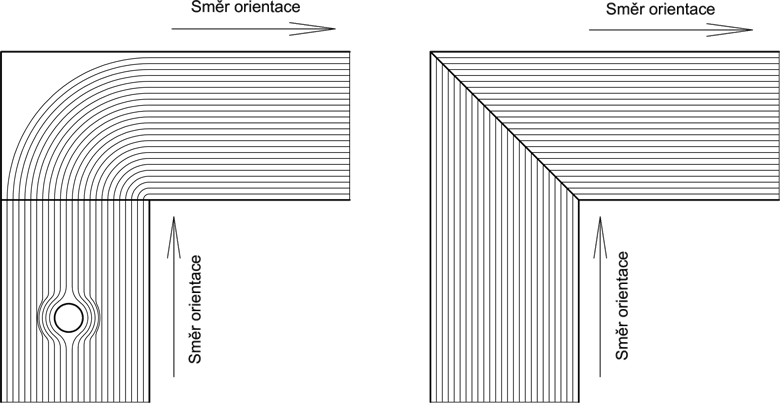
Obr. 5 Spoj s pravým úhlem hrany včetně ovlivnění magnetického toku dírami v plechu b) Spoj s hranou střiženou pod úhlem 45°
Spoj natupo, non step-lap, step-lap
Metoda natupo spočívá ve skládání plechů na sebe tak, že všechny vrstvy jsou totožné a hrany ve spoji tvoří spojitou plochu, viz obr. 5 uprostřed. Tato metoda je však v moderních velkých magnetických obvodech nepoužitelná, protože magnetický tok nemá jinou cestu než přes vzduchovou mezeru vzniklou ve spoji a tím vznikají významné ztráty.
Tyto ztráty se dají eliminovat metodou přeplátování, která se dá rozdělit na non step-lap a step-lap. U stavby přeplátovaného jádra jsou plechy skládány tak, že mezery ve spojích mezi sloupky a jhy jsou překryty plechy další vrstvy. Tím, jak jsou plechy stupňovitě přesazeny a skládány jeden na druhý, mezery ve spojích netvoří rovnou plochu. Velikost přesahu se pohybuje okolo 15 do 20 mm. Ve spojích tak magnetický tok může pokračovat na sousední plech, aniž by procházel přes vzduchovou mezeru, která je přímo v jeho cestě. Mezera ve spojích hraje velkou roli ve velikosti ztrát a proudu naprázdno. Ve srovnání s nulovou mezerou je nárůst ve ztrátách 1 až 2 % pro 1,5 mm mezeru, 3 až 4 % pro 2,0 mm mezeru a 8 až 12 % pro 3 mm mezeru. Tyto čísla zdůrazňují, jak je důležité minimalizovat mezery při skládání plechů.
Metoda step-lap je charakterizována odstupňovaným přesahem plechů ve spoji, kde je odstupňování získáno rozdílnými délkami plechů v každém kroku. Počet kroků odstupňování bývá obvykle mezi 5 až 8 a každý krok má jeden nebo více stejných plechů na sobě. Tyto kroky jsou na sebe poskládány tak, že spoj v řezu připomíná schody. Plechy, které tvoří jeden cyklus kroků na jednom kusu (jho nebo sloupek), se nazývají paket (spoj dvou paketů je vidět vpravo na obr. 6.) a ty se opakují tak aby byla dosažena požadovaná tloušťka stupně. Šířka stupně kruhového jádra se snaží být navržena tak, aby obsahovala ideálně celočíselný počet paketů, případně aby poslední paket byl více než poloviční z důvodu efektivity skládání jádra.
Non step-lap je ve skutečnosti předchůdcem step-lapu a je to nejjednodušší forma přeplátování, protože má pouze dva kroky, takže plechy mají pouze dvě konfigurace (viz obr. 6. vlevo). Více kroků oproti jednoduchému překrytí však zajišťuje plynulejší přechod magnetického toku spojem a snižuje v něm tak ztráty, proto se non step-lap v Evropě a všude tam, kde jsou kladeny velké nároky na nízké ztráty, nepoužívá. S jádrem non step-lap jsou distribuční transformátory vyráběny například v Indii.
Na základě zkušeností se ukázalo, že čím méně plechů jeden krok přeplátování obsahuje, tím menší ztráty vznikají. Např. konstrukce se dvěma použitými plechy v kroku mají ztráty nižší o 3 až 4 % oproti čtyřem plechům v kroku a o další 2 až 3 %jsou ztráty nižší pro jeden plech. Na druhou stranu s klesajícím počtem plechů v kroku narůstá čas na skládání jádra. V praxi se proto osvědčilo použití dvou plechů na krok a např. ve firmě Elpro-Energo s.r.o. se používá step-lap se 6 kroky po 2 plechách, přesah mezi kroky je 3,6 mm, takže přesah plného paketu je 18 mm (s výjimkou plechu o šířce 50 mm, kde je z technologických důvodů možný přesah nejvíce 2,8 mm na krok).
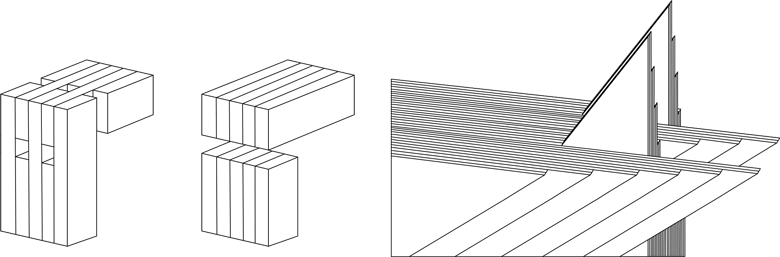
Obr. 6. Detail spojů, zleva non step-lap, natupo a step-lap (s pěti kroky)
Přínos step-lapu oproti non step-lapu
Když se magnetický tok v jádře přiblíží ke vzduchové mezeře v rohovém spoji se jhem, má dvě možnosti – buď přejde vzduchovou mezerou ve spoji, kde je permeabilita mnohem menší (=1), takže magnetická vodivost vzduchu je mnohem menší. Druhou možností pro tok je, že protne izolaci mezi plechy a přejde do sousedního plechu ve vertikálním směru (směr kolmý na směr orientace válcování plechů) nad nebo pod, kde je permeabilita v řádu 104 a tedy magnetický odpor je mnohem menší.
Tok jednoznačně volí druhou možnost, tj. přejde skrz izolaci do plechu nad nebo pod ním. Nicméně když je CRGO nasyceno při magnetické indukci přibližně 2 T, je to mezní stav, který dovoluje přejití toku i přes vzduchovou mezeru ve spoji. Uvažujme jádro, které pracuje při velikosti amplitudy magnetické indukce 1,7 T. Jak se magnetický tok přibližuje k mezeře ve spoji, musí si vybrat mezi možnostmi 1 a 2 uvedenými výše.
Když se veškerý tok přesune do sousedního plechu nad nebo pod, v jádře složeném metodou non step-lap, kde jsou pouze dvě konfigurace plechů, bude magnetická indukce v překrývajícím plechu o hodnotě 3 · 1,7 / 2 = 2,65 T (viz obr. 7a), což způsobí nahromadění toku a velmi překročí hranici nasycení CRGO plechu (která je přibližně 2 T). Tím pádem u non step-lap spoje část magnetického toku přejde do sousedních překrývajících plechů, avšak část toku bude muset také přeskočit vzduchovou mezeru (což je možnost 1). Dokonce i tok, který přechází do připojených plechů, zvyšuje v nich magnetickou indukci nad úroveň nasycení, což také přispívá k nasycení materiálu ve spojích a tím zvýšení ztrát naprázdno.
Tok, který přejde přes vzduchovou mezeru, přispívá k úbytku magnetického napětí a na krytí těchto ztrát vyžaduje větší proud naprázdno, aby se dosáhlo požadované magnetické indukce v jádře. Nadměrné nasycení materiálu v rohových spojích dále vede k vyšší magnetostrikci jádra, což je hlavní příčinou hladiny hluku v transformátoru.
Nicméně u metody step-lap je situace jiná. Tok, který se přibližuje ke vzduchové mezeře, má pro přenesení mnohem více možností, jak je možné vidět na obr. 7b, a to jednoduše proto, že se zde vyskytuje více vrstev (kroků) plechů, do kterých se může tok přerozdělit. Jak je možné vidět ve schematickém znázornění jádra o šesti krocích, tok má úměrně šest možností pro překročení místo jen dvou, a proto je zde mnohem více rovnoměrné rozložení toku ve spojích, což vede k mnohem méně toku, který přeskočí přímo přes vzduchovou mezeru. Tím je příspěvek ztrát v rohových spojích menší a magnetická indukce zde zůstává okolo hranice nasycení, tedy 2 T.
Přechod z non step-lapu na step-lap snížil činitel přídavných ztrát naprázdno o 5 až 8 %, kromě ztrát značně klesl proud naprázdno a také hladina hluku transformátoru. Step-lap však pro svou výrobu vyžaduje vysoce přesnou automatickou vysekávací linku, jedná se ale o velkou investici.
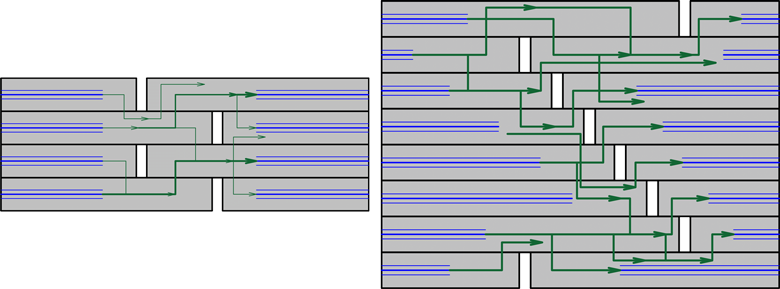
Obr. 7 Cesta magnetického toku ve spoji pro a) Non step-lap b) Step-lap
Zdroj: MRAJCA, Miroslav. Návrh olejového distribučního transformátoru. Brno, 2021. Dostupné také z: https://www.vutbr.cz/studenti/